Technologies having a facility which is ideal to manufacture the Custom built heavy machines which includes
- Design department to transform the Concept and customer requirements to a Proposal and detailed manufacturing drawings.
- Manufacturing and assembly facility with proper material handling facilities keeping in the Safety of the employees.
Area
- Total Area: 12000 Sq Ft
- Built up area: 10000 Sq Ft
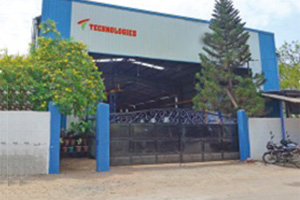
Front View
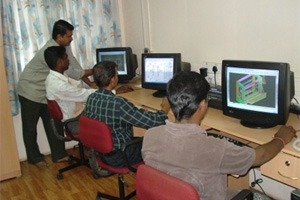
Design Department
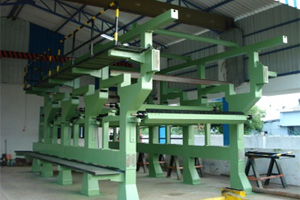
Assembly
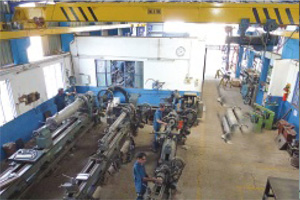
Machine Shop
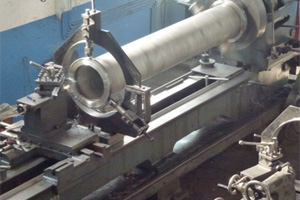
Seven Meter Mathe
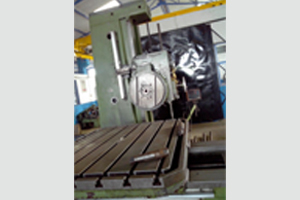
Horizontal Boring Machines
Material handling
The Work shop is installed with 5 Tonne EOT crane and 2 Ton EOT Cranes
Power back up
To overcome the power failure, the Kirloskar Genset is installed
Dedicated Vendor Units
Technologies always believes in the Outsourcing for Cost benefit, and Vendor development and using 10 dedicated self certified Quality vendors for Components machining apart from the in-house facilities.
Process Flow
Facilities for Production & QC
Pattern & Methoding
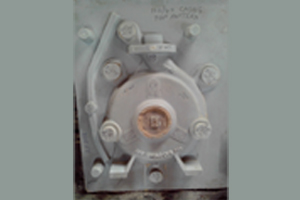
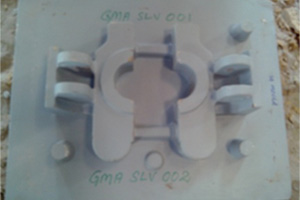
Facilities for Production & QC
- The pattern making is outsourced
- Methoding and inspection is done upon completion of pattern
- The pattern mounting with the base plate with proper methoding is carried out before moulding
Moulding & Core Making
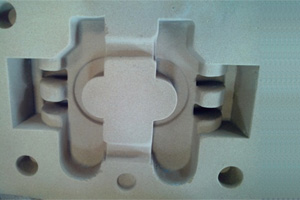
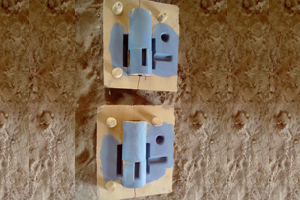
Facilities for Production & QC
- Process used for moulding is CO2
- The mould sample is tested for a batch with a mould hardness tester
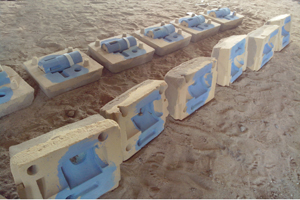
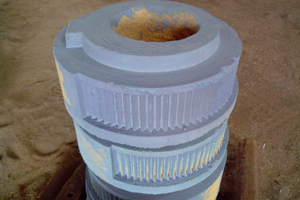
Facilities for Production & QC
- The boney meter is used to check the sodium silicate oil and the coatings.
- The quality of raw materials are checked before taken into the process.
Melting & Pouring
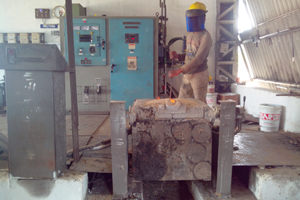
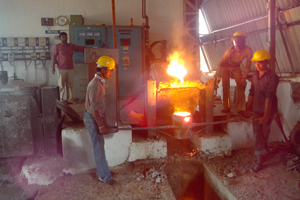
Facilities for Production & QC
- 2 nos of Induction furnace
- 300 kg and 100 kg
- Inductotherm make
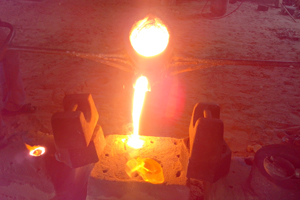
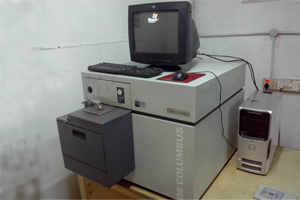
Facilities for Production & QC
- The metallurgy is controlled in process using the Spectrometer
- Before tapping the metal,the Pyrometer is used to check the temperature which ensures proper flow of liquid
- The necessary chemicals are used to Impurities from the metal before tapping
Knock out & De-Coring
- This process is done after ….Time after Pouring
- The necessary hand tools and Pnuematic equipments are used to ease Process.
Cutting
- The gas cutting is carried out for the Carbon and alloy steel and arc cutting is Done in case of Stainless steel
- The heat nos are punched immediately in castings non machining area after cutting process.
- Helps in traceablilty of quality records before and after sales.
Heat Treatment
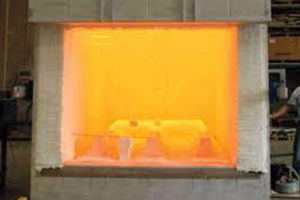
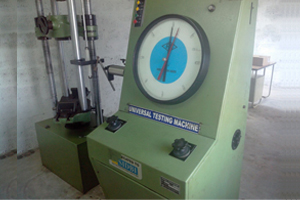
Facilities for Production & QC
- The heat treatment process is outsourced from a dedicated vendor
- The test bar for every melt is poured and the same is machined and subjected to mechanical testing, Impact and Harness testing
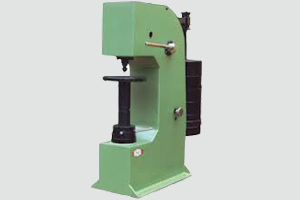
Facilities for Production & QC
- Inductotherm make
- The UTM, Brinnel hardness and Impact tester are erected to perform these Quality control measures
Fettling and Shot Blasting
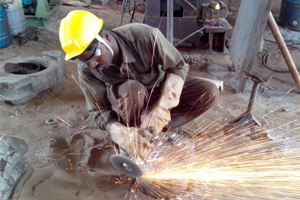
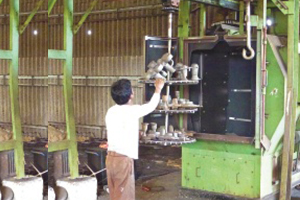
Facilities for Production & QC
- The fettling is carried out with the necessary swing and profile grinding tools and finally the castings are put into the NDT testing – MPI, RT & UT
- According to the customer requirement(100%, 50 %, Each one per size / Class.)
Pre Delivery inspection report
- The dimensional and visual inspection and Documentation is carried out and the items are shot blasted before delivery to customer
- The Documentation requirements of the customers are fulfilled as per the contractual requirments and set of documents are sent to customer along with the supplies.